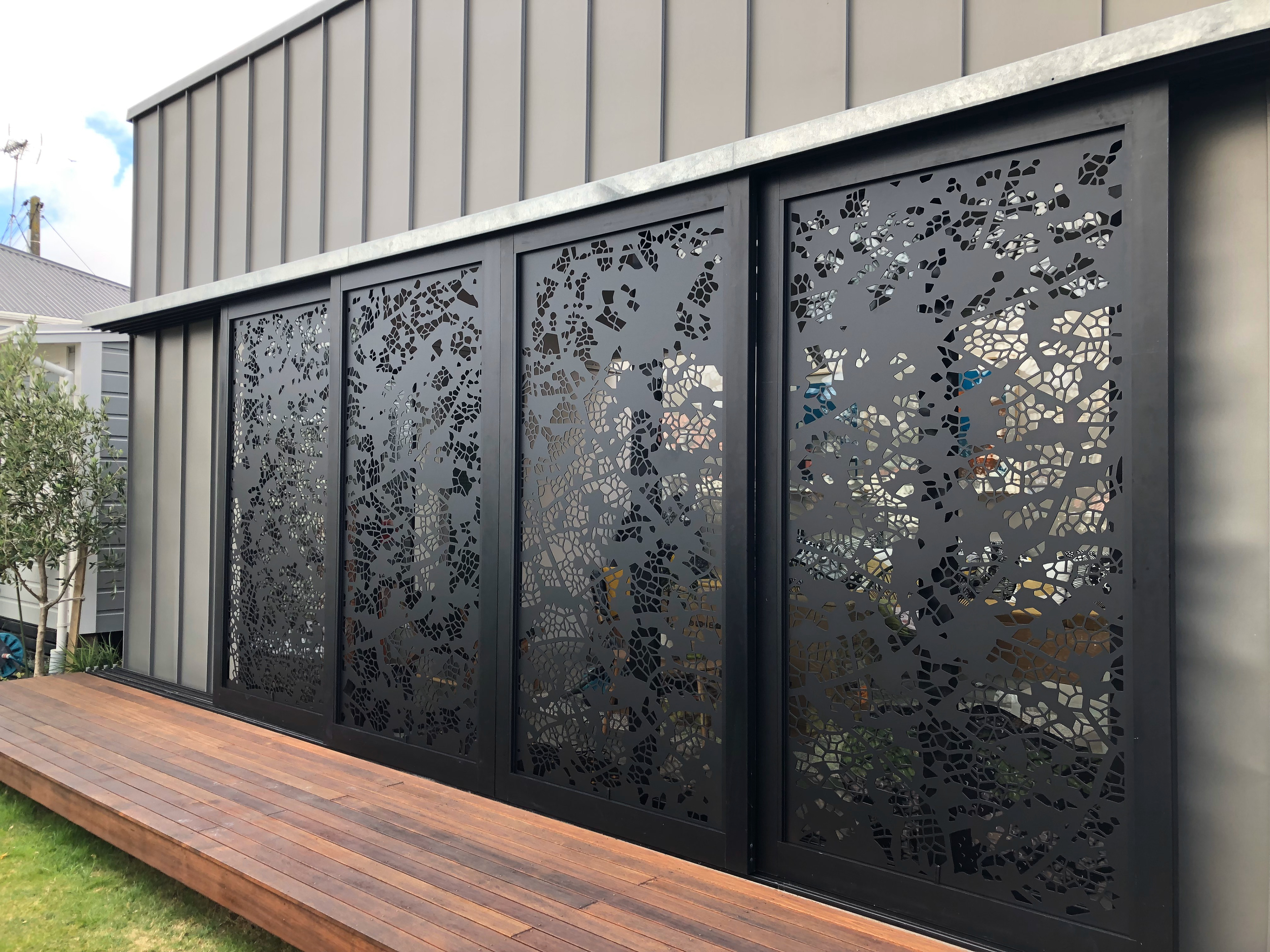
Leaf Skeleton – residential screens
Client: Private residence
Role: Design and production
Dimensions: Four sliding panels – 5.1m × 2.5m total
Medium: Vector-based design for laser-cut steel fabrication
Spatial design, 2019
Role: Design and production
Dimensions: Four sliding panels – 5.1m × 2.5m total
Medium: Vector-based design for laser-cut steel fabrication
Spatial design, 2019
Collaboration and process
Inspired by the structure of a leaf skeleton and the way light filters through a forest canopy, this project brings organic patterning into a contemporary architectural setting.
The design process was collaborative from the outset, involving close coordination between architect Michael Gould, fabricator Hartmut Reichelt, the client, and myself. Together, we developed a pattern that felt harmonious within its suburban context—visually soft, responsive to light, and thoughtfully integrated with the building’s cool steel exterior.
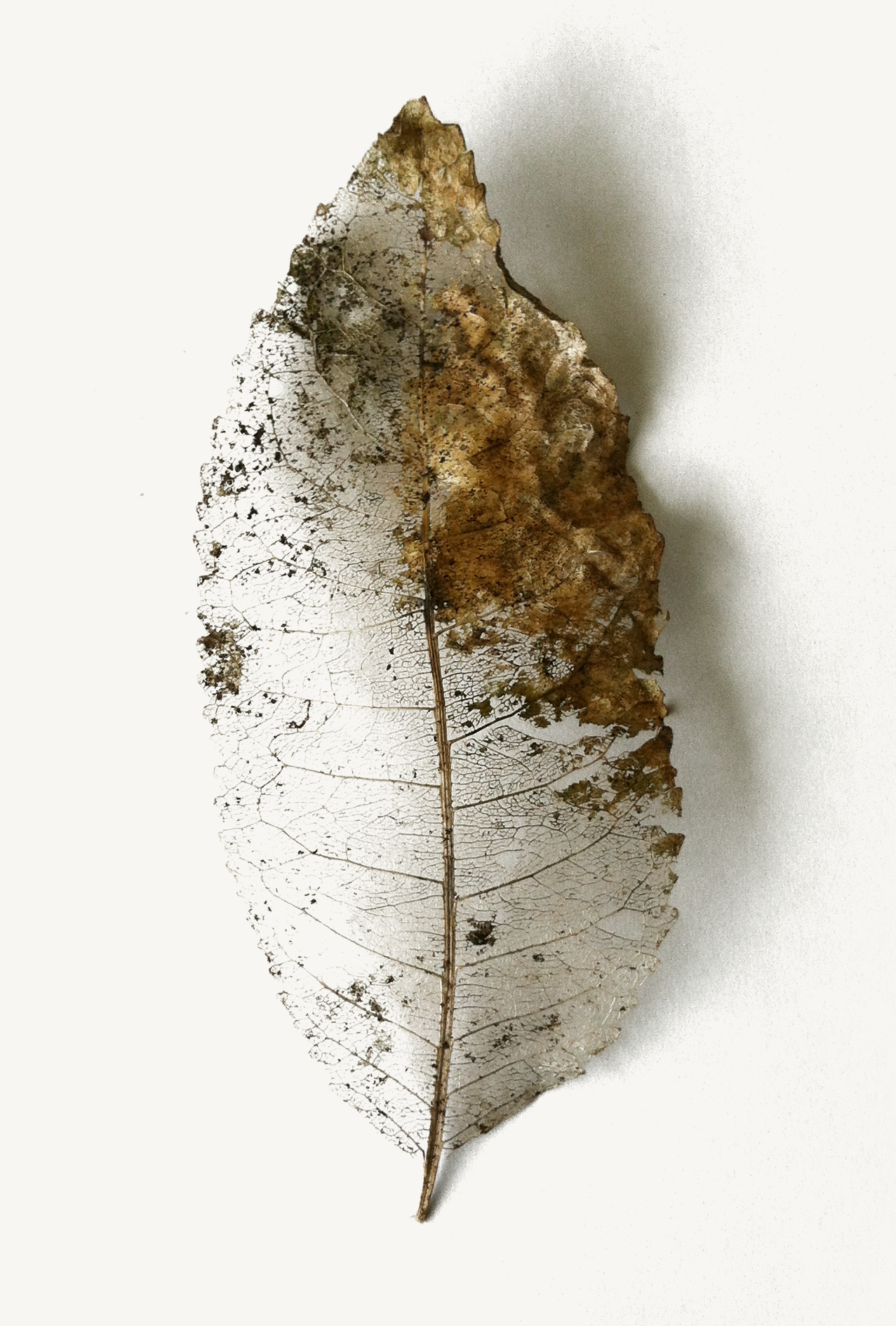
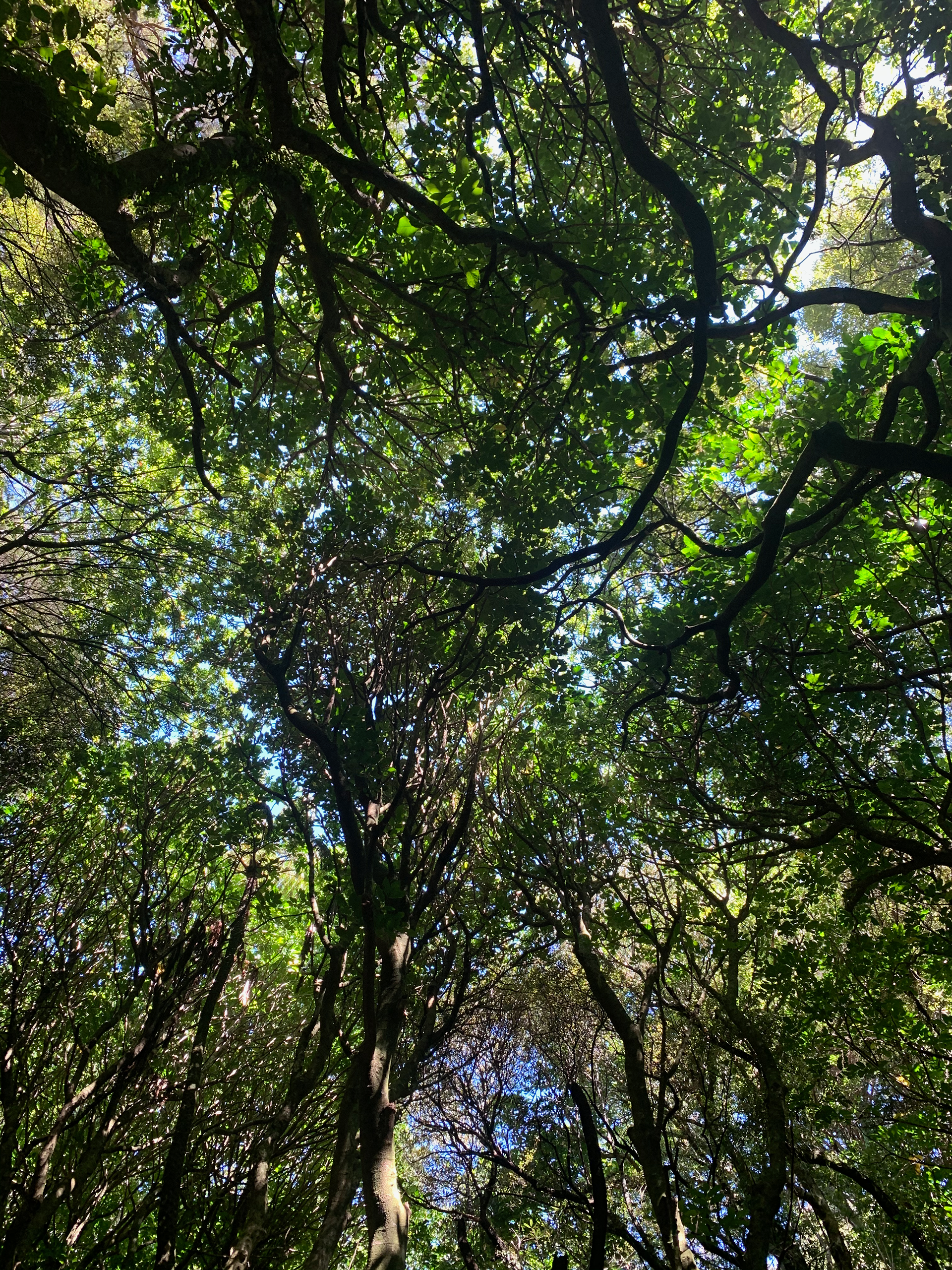
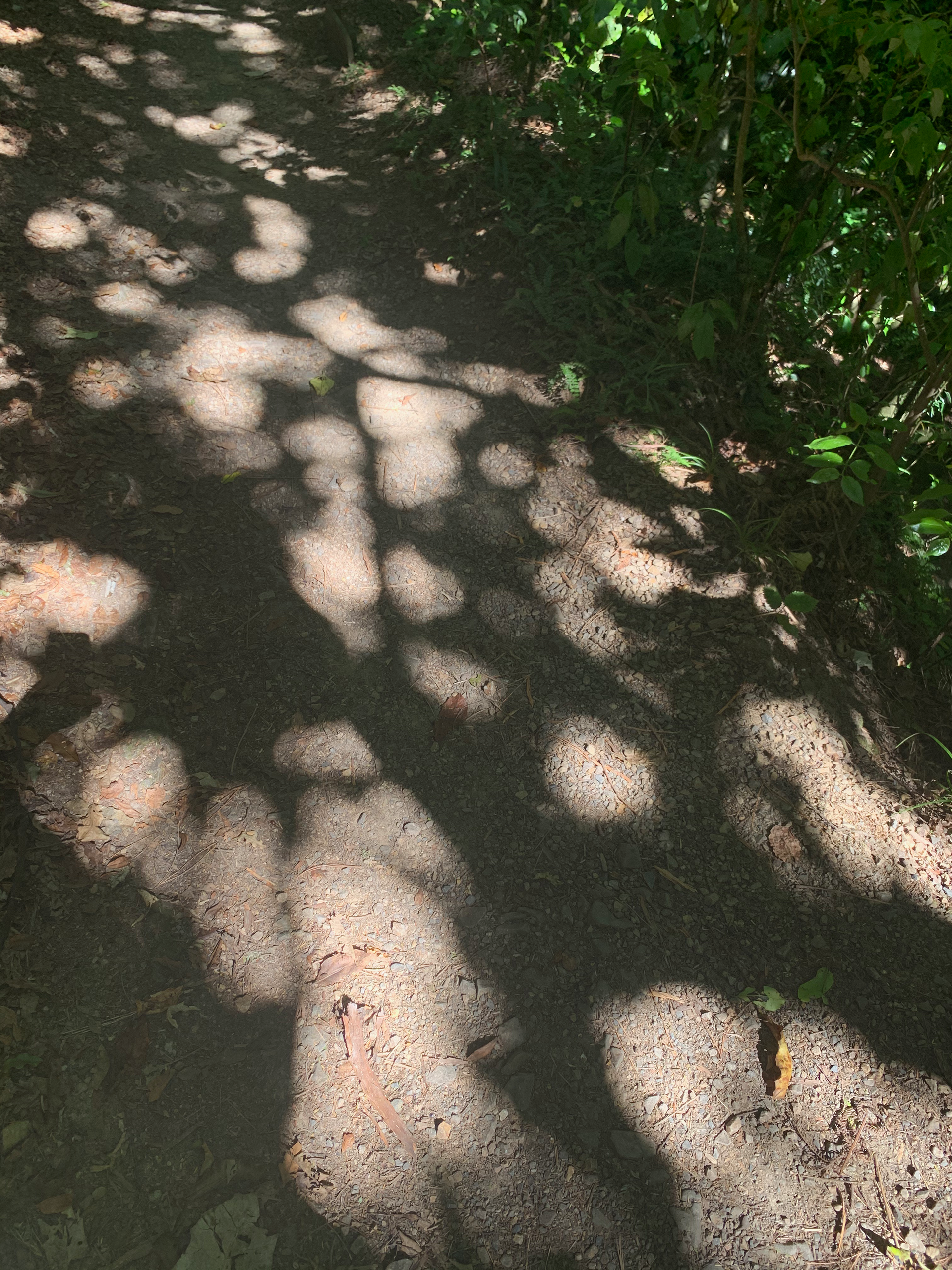
Refining for fabrication
I worked closely with fabricator Hartmut Reichelt to simplify and strengthen the pattern—making sure the steel could hold its shape and the design could be cut cleanly. His feedback helped shape the final version, tweaking line weight, spacing, and load resilience.
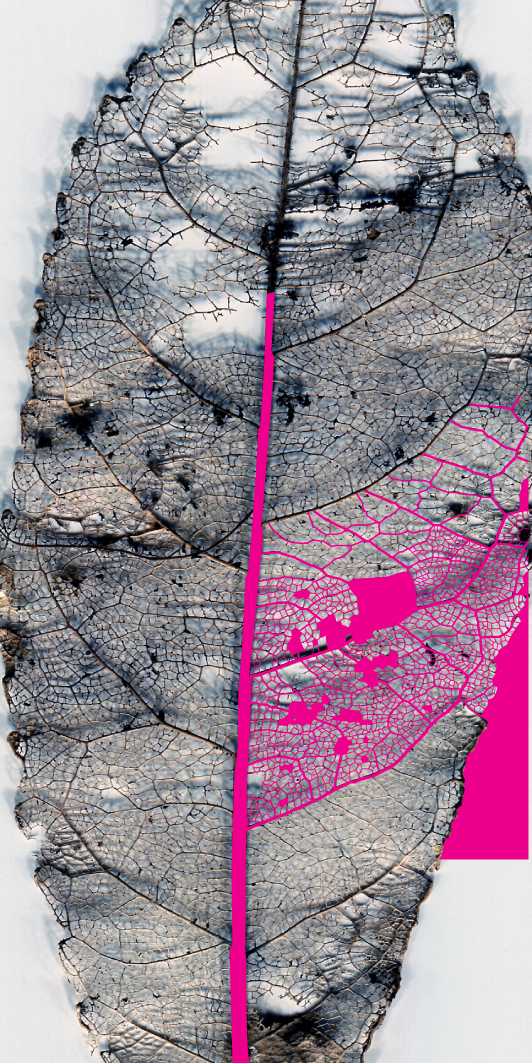
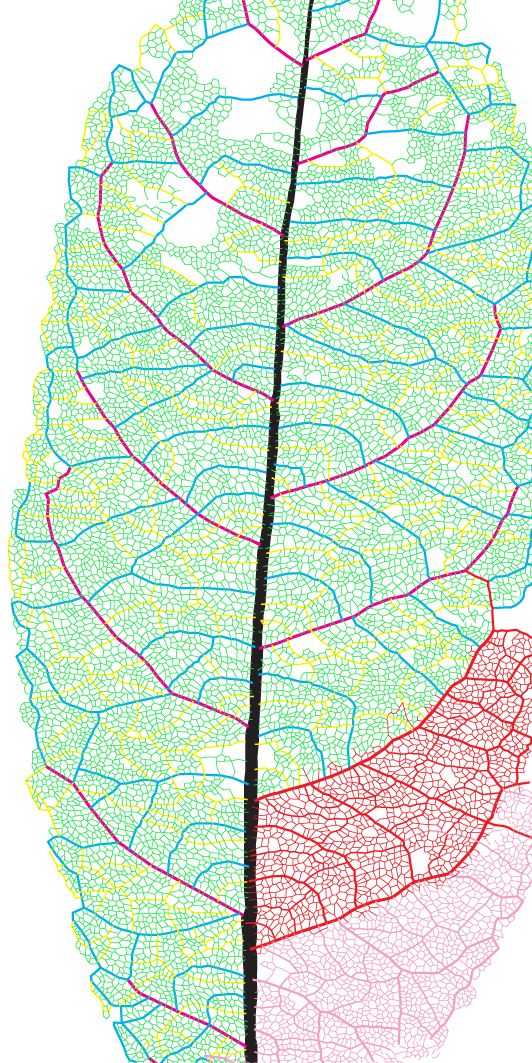
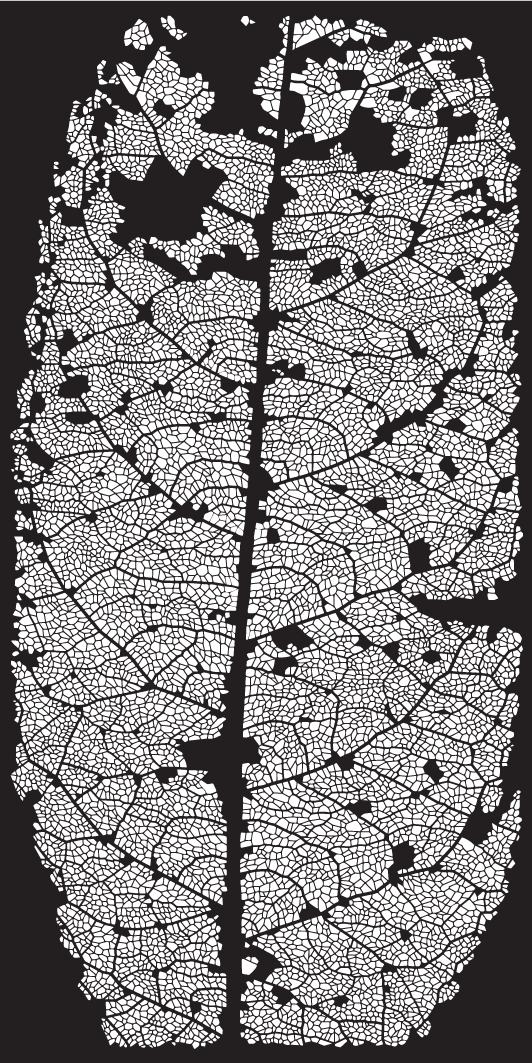
Balancing detail and practicality
The first full draft of the pattern looked great—but wasn’t especially practical. It pushed the laser cutting time, cost, and structural stability. Rather than compromising the design entirely, we adjusted it: less cutting, fewer holes, and a better balance between detail and durability.
From file to finish
These screens had to slot precisely into a pre-existing aluminium door and glazing system. That meant working closely with Michael to get frame tolerances right, consider thermal movement, and allow for a clean finish. A custom aluminium shim was used to mount the panels like standard glazing, so everything felt seamless.
Installation and on-site coordination
I stayed involved through fabrication and final installation, making sure the panels were produced in the correct sequence. Michael and Hartmut refined the glazing and install details, and I supported the coordination to ensure everything came together smoothly.
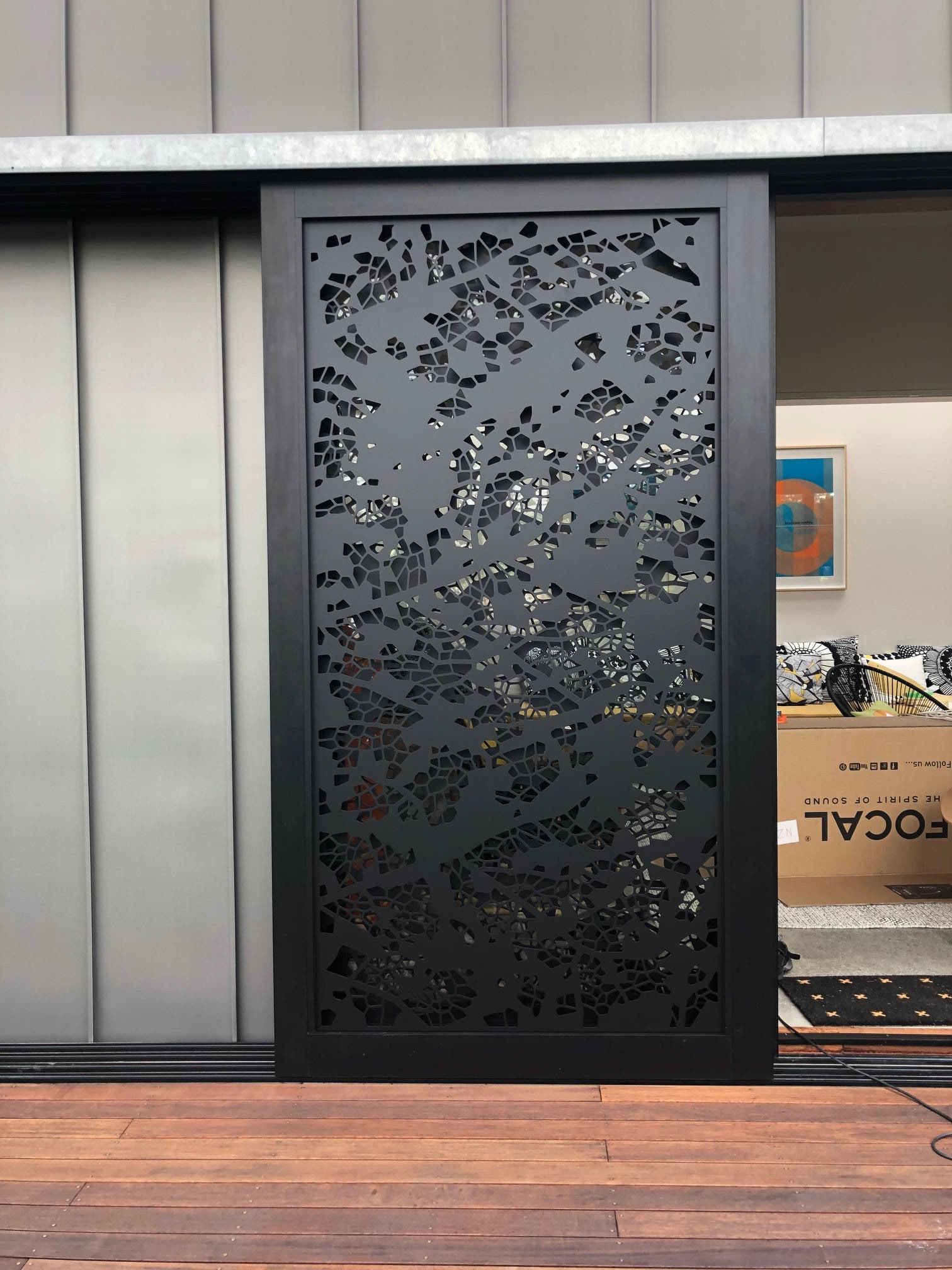
Designed in close collaboration with the client, architect, and fabricator, the result is a functional and expressive feature that balances craft and digital precision. This was one of those projects where the result was better because of the team behind it. Everyone brought care, clarity, and attention to detail. What began as a complex idea, was shaped through dialogue, iteration, and trust in the process.
Thanks to Michael Gould (architect), Hartmut Reichelt (fabricator), and the wider team.